Solutions to Eliminate the Over-Engineering of Motion Control Systems
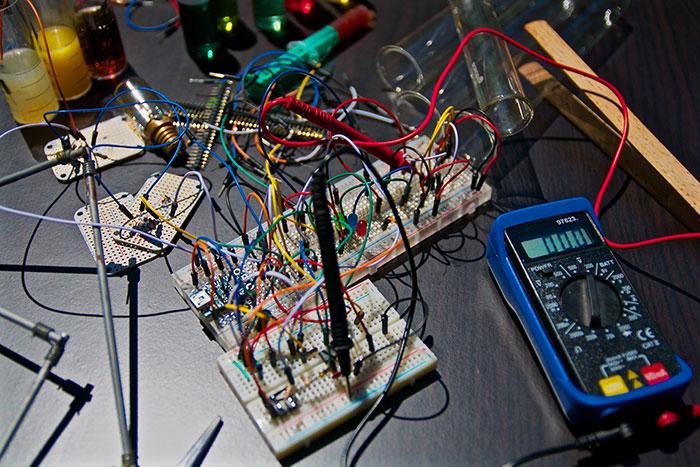
Solutions to Eliminate the Over-Engineering of Motion Control Systems
Over-engineering has been part of creating an application solution, particularly with motion control systems, from the beginning. Make it last, might have been the call to action. A small bit of over-compensation provides a sense of comfort and security, a feeling that the product will outlast the users’ invisible criteria for value. The solution where even slight over-engineering makes the difference in perceived value is only the beginning of the problem.
When a motion system has multiple components, and even a small percentage of those components are over-engineered, product costs can escalate, space allocations can grow, and specifications can be pushed beyond the limits of the user's needs. Pitching one component against another easily increases the chances for over-engineering, and over-engineered motion systems often have an increased number of components, introducing more points of failure. Any or all of these factors will have an effect on the sales of the end product.
Challenges to Over-Engineering
One of the more positive, but also primary challenges to over-engineering is the conscientious engineering team. There are many teams like this in the motion control business. Those who truly want the product to perform well, be reasonably priced, and be as compact as necessary. Such a team goes out of their way to research and secure components for their motion system while trying to balance all the needs of the system in a way that feels right to them and will end in a satisfied customer experience. All good intentions.
During early research is where major decisions are made, one of which is whether to find the right manufacturers for the components you are looking for, or to contact an engineering company that has a lot of expertise in your particular application and that can help you to fabricate the exact system you are looking for. This is a big decision and should not be taken lightly.
A lot of manufacturing companies have a line of standard products—such as motors or controllers for your motion control application. As an engineer, it is possible to compare and select from these offerings, pitching speed against torque or accuracy. The tendency is naturally to always select from a specification sheet that offers more than your exact needs (see Sidebar I: “Three Ways to Increase the Torque of your Stepper Motor”). Your other option at this point is to check in with the manufacturer to see if they can customize a device for you. As you wait for the quote to do so, you cringe at how much it could raise the price, especially for small quantities.
For the engineering team that researches an outside engineering company that can build from scratch the component needed, there is already an expectation of a high cost for engineering and possibly delays in delivery. The other problem with this approach is whether or not the engineered product will realistically integrate with all the other components of your final motion control system. Once again, many engineering teams will err on the side of over-engineering if there is any doubt about the project at all.
Furthermore, every engineering team working today has to consider repair and maintenance costs as well as development costs in their final choice of solution. In the trend toward quality and reliability, machine breakdowns become too costly, both in direct expense associated with warranty work and in the loss of reputation. These costs dovetail right into the customers’ perceived value of the product and manufacturer and must be considered very closely while your project is in the early phases of design.
What Engineering Teams Are Looking For
Valuable assets to any engineering team in a competitive market such as motion systems include competitive pricing, which includes the cost of development, cost of manufacturing, and cost of maintenance and support; the assurance of quick delivery even during a spike in needs; and expertise in the product area being represented.
When it comes to motion control systems, you’ll want to look at a company’s performance and reliability characteristics and standards, their breadth of product lines based on your possible future needs; and a willingness to work engineer-to-engineer to solve your application’s particular challenges. Once you’ve found the manufacturer who has these assets, you are able to get the help you need to optimize your motion system for performance, customize it for best fit, and produce a rapid prototype (see Sidebar II: Rapid Prototyping of Linear Drives) of the component for evaluation and testing purposes.
What the right partner might look like is not just a product manufacturer and not just an engineering company, but a solutions-focused engineering and manufacturing company. You want to find a company that addresses the whole system and not just a few of the component parts. You want a company that can provide reduced overall developmental costs, reduced time to market, reduced overall system cost, and provide on-time delivery of components with scalable manufacturing to satisfy your needs. All this can be done, and should be done, within a quality control system to ensure consistency of product and eliminate the potential for specification drift over time.
Three Ways to Increase the Torque of your Stepper Motor
Torque is the rotational force generated by the electromagnets in the stator of the motor interacting with the permanent magnets in the rotor of the motor.
The first way to increase torque would be to increase the magnetic field in the rotor of the motor. Since most motors today use neodymium rare earth magnets in the rotor—because of their high magnetic field strength—the grade of those magnets can have an effect on torque. Neodymium magnets are graded by the materials they are made of and carry a rating such as N35, N42, and N52, which is currently the highest grade available. If you assume that the permanent magnet remains at the same strength, torque is proportional to the number of winding turns on the stator pole multiplied by the input current.
So, the second method used to increase torque in a stepper motor is to increase the input current. Since higher current means a higher magnetic force in the stator, this too will increase the overall torque of the motor. As can be expected, you can only increase current to a particular amount before you damage the motor.
Along these same lines, increasing the number of winding turns in the stator allows for more magnetic force to be available with a steady current input. Most manufacturers design their motors at the maximum number of winding turns possible for a particular size. This means that increasing winding turns requires that the manufacturer must also increase the size of the motor.
Another way to increase torque is to operate your stepper motor in a bipolar series or parallel configuration rather than a unipolar or bipolar half-coil configuration. This allows the electrical properties of the winding, such as voltage, resistance, and inductance, to be altered—which can affect both the speed and torque performance of the motor.
Rapid Prototyping of Linear Drives
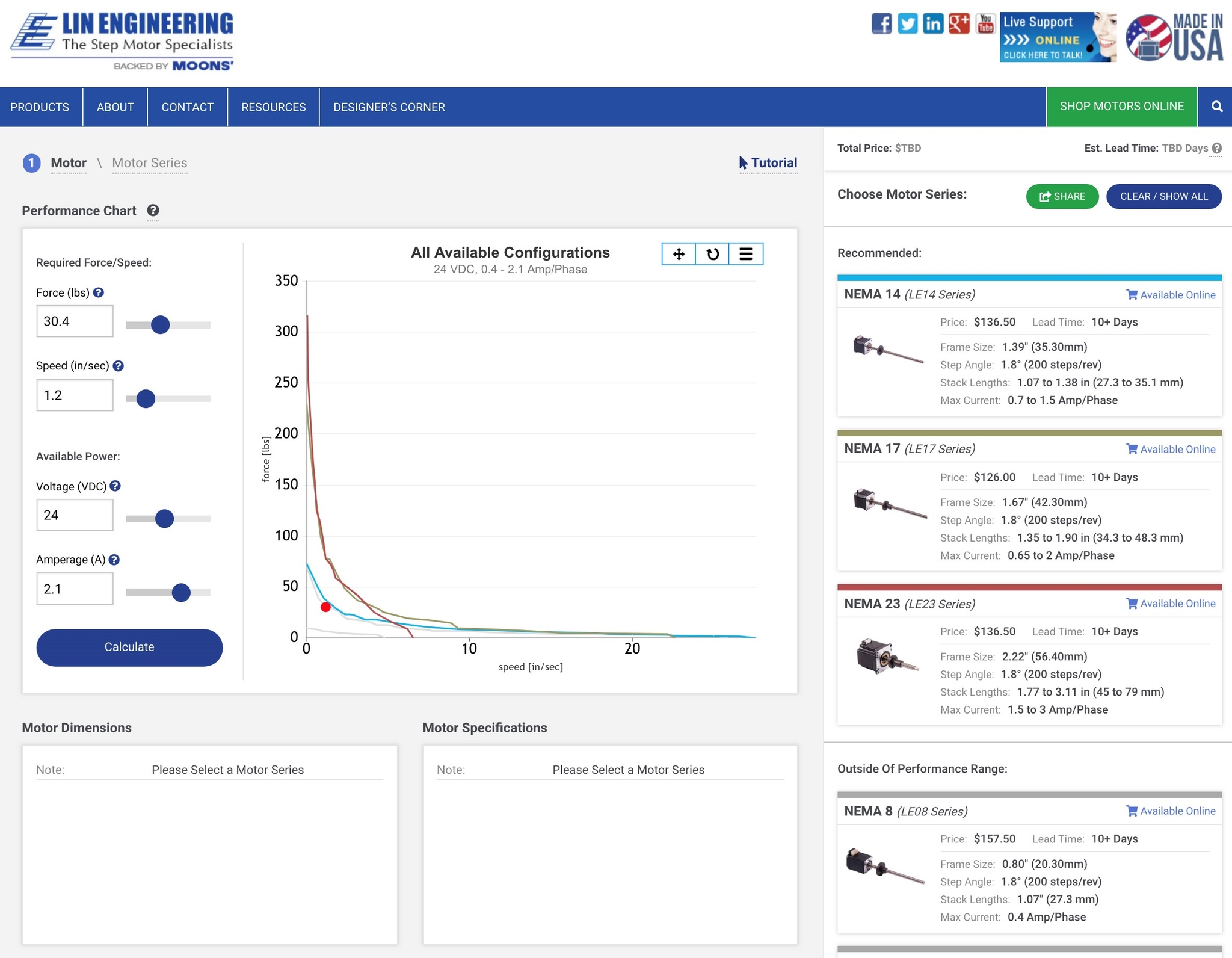
In many advanced applications, there is a need for a prototype of specific components in a short amount of time so that evaluation and testing can be completed, the product can be adjusted, and it can eventually be ordered. There are few places where rapid prototyping for linear motion devices is possible.
Modular product structures are not new, but when you’re talking about a complex product such as a linear drive for a motion system, there are a lot of interactive components to consider. If you don’t want to be hounded by a salesperson, you might consider looking over Lin Engineering’s Rapid Prototype Configurator, where engineers can compare different components while honing in on their specific application needs. The company’s new Configurator is one way Lin Engineering is providing services to engineers focused on their needs and not just the products the manufacturer wishes to sell.
News
Continue Reading
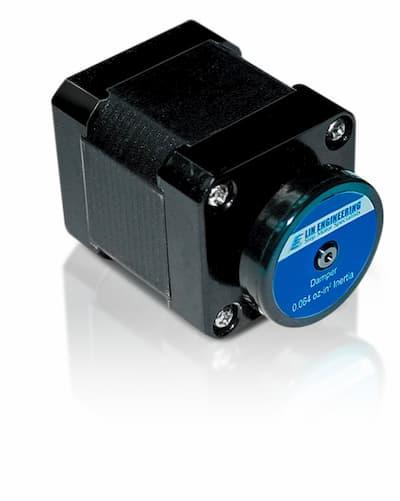
Tips on How to Reduce Stepper Motor Resonance
Noise reduction can be a challenge when designing in stepper motors for certain applications. This resonant vibration often produces adverse effects that are easily eliminated once you understand what changes to make.
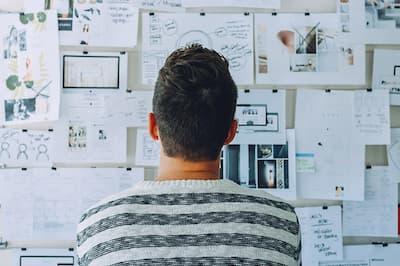
Tips for Decreasing Points of Failure in Motor Systems Design
Engineers need a way to move things within their assemblies in a controlled manner. Yet, the more components used, the choice of component, and wrong budget choices, the more points of failure are present. This article will cover some of the more prevalent concerns when designing your next motion system.