Reducing Electric Motor Weight
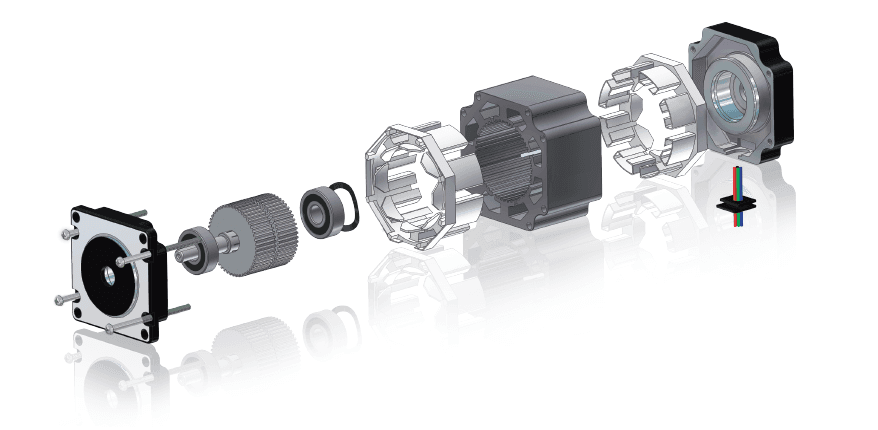
Reducing Electric Motor Weight
Depending on the type of system you are designing for and the potential environment it will be operating in, motor weight can be very important to the overall cost and operational value of your system. Motor weight reduction can be addressed from several directions, including general motor design, efficient component production, and materials selection.
Proper Design Elements
Designing the most efficient motor is a critical aspect of weight reduction. Because most motors are designed for broad use, the right motor for a particular application is often larger than what is actually needed. To overcome this challenge, it is important to look for companies willing to alter in a semi-custom manner everything from the motor windings and magnetic components to their frame size. To be sure you have the correct winding, you’ll want to explore your specifications so that you are able to maintain the exact torque and speeds needed for your application.
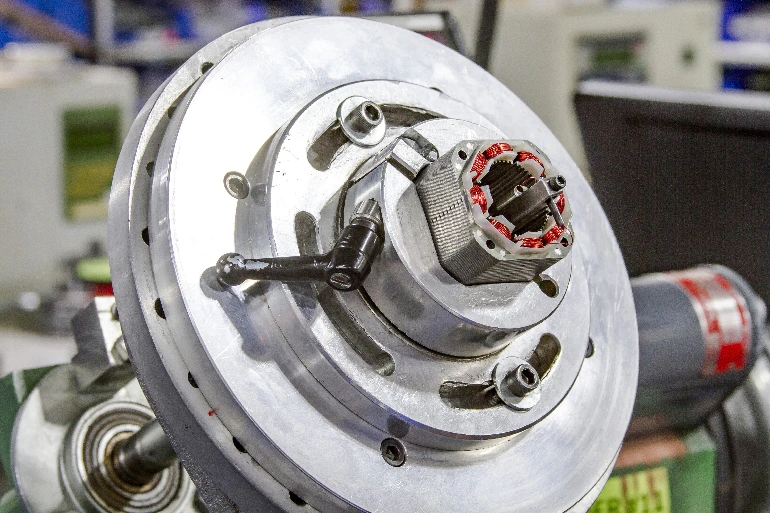
Besides adjusting your windings, manufacturers have the ability to change the magnetic design of your motor based on a variance in magnetic permeability. The use of rare earth magnets that are placed properly between the rotor and stator can help to increase the overall torque of the motor.
As long as your application does not have to adhere to strict motor frame sizes, such as NEMA, the motor frame can be adjusted to fit your needs. Such customizations are less often required, but they are available from some manufacturers if volumes are high enough. Then again, manufacturers also offer frameless motors which can have an effect on motor weight by eliminating the frame altogether.
Efficient Component Production
What we’re talking about here is the ability for manufacturers to continually upgrade their own equipment to produce motor components that are held at higher tolerances, eliminating thicker walls and dense areas once used as a safety margin against breakage. As each component is redesigned and manufactured using the latest technologies, weight can be shaved off in multiple places from which magnetic components are incorporated, to insulation and coatings, to frames and motor shafts.
Material Selection
Material selection has an overall effect on motor operation, efficiency, as well as weight. For the clearest example, this is why so many manufacturers are using aluminum frames rather than stainless steel. When you consider the internal design elements of a motor, you get even more exotic. Manufacturers have continued to experiment with materials that offer both electromagnetic and insulation-based characteristics.
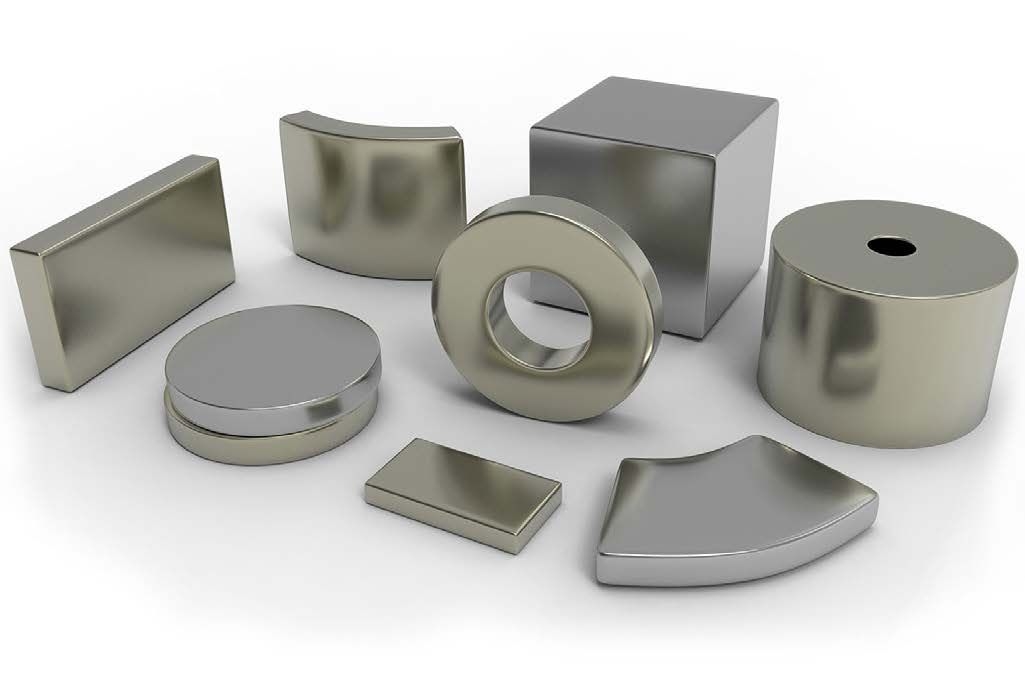
Manufacturers are using a wide variety of different composite materials as well as lighter metals that provide a lightweight alternative to steel components. For installation purposes, a wide variety of reinforced plastics, polymers, and resins are employed depending on the specific characteristics the user is requesting for their final motor.
As motor designers are continually experimenting and researching alternative components, including less dense coatings and resins used for sealing purposes, they infuse new life into the production process—often affecting motor weight.
Conclusion
Motor manufacturers continue to research and experiment with a wide variety of designs, component production capabilities, and materials in such a way as to deliver greater performance and efficiency at a reasonable cost to the user. When it comes to providing the right motor for the right application, companies like Lin Engineering have explored all aspects mentioned in this article. They are known for designing their motors in a modular fashion so that they can key into their customers’ needs and provide a motor that is right for most applications.
News
Continue Reading
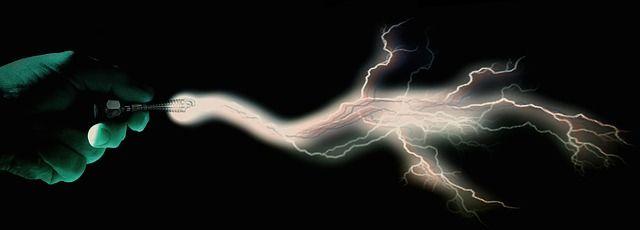
Reduce Your Chances of Electric Motor Overheating
Motor winding life is an important factor when it comes to decreasing motor failure rates. As with any other factor in a motor-driven system, there are steps that can be taken to decrease heat generation and therefore provide longer life to your motors.
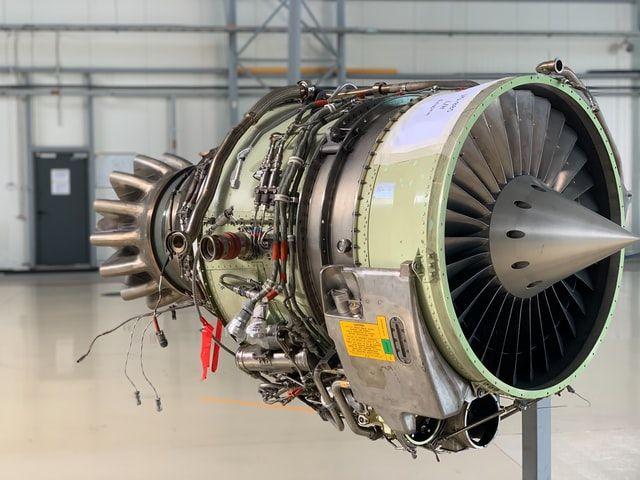
Aviation Applications and IP Rated Motors
Most aerospace industry components—including those used in general aviation applications—are exposed to the elements repeatedly throughout their use. This is particularly true for motors since motion control of everything from fuel lines and ailerons to instruments and controls are implemented both inside and outside of the aircraft.