productsstepper motorsspecialty motorsvacuum rated motors
cleanroom stepper motors
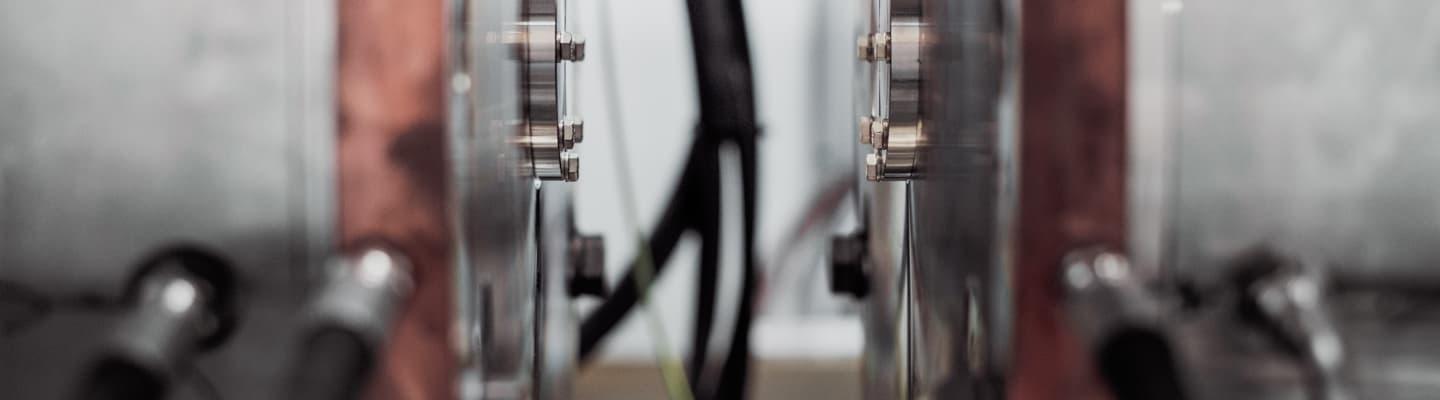
Low Outgassing Stepper Motors For Cleanroom Applications
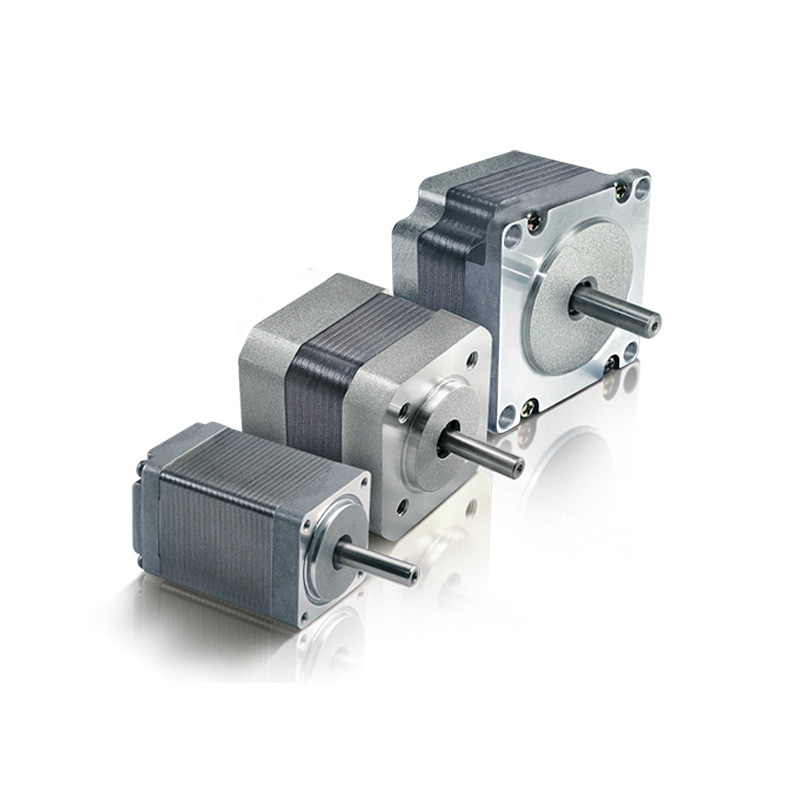
Vacuum-rated stepper motors are often a necessary requirement when working in a cleanroom environment. Similar to their use in the industrial and aerospace vacuum environments, you’ll need to consider outgassing contamination as a major challenge. Outgassing occurs when gasses and particles that are trapped inside paints, coatings, and greases, are released into the environment and introduce unwanted contaminants. Vacuum rated stepper motors must be designed using low-outgassing materials in order to minimize the outgassing problem, which makes it ideal for cleanroom environments too.
Vacuum compatible motors, such as our 211 Series (NEMA 11), 4118 Series (NEMA 17), and 5718 Series (NEMA 23) motors, manage outgassing through our proprietary motor assembly process designed specifically for vacuum motors. By using low-outgassing materials during the manufacturing process, our products also reduce the number of contaminants that are able to enter the system.
We’ve compared our vacuum compatible motors against major competitive devices in a positive flow chamber that measured outgassing levels. Our vacuum compatible motors repeatedly outperform the competition. Contact us for specific information.
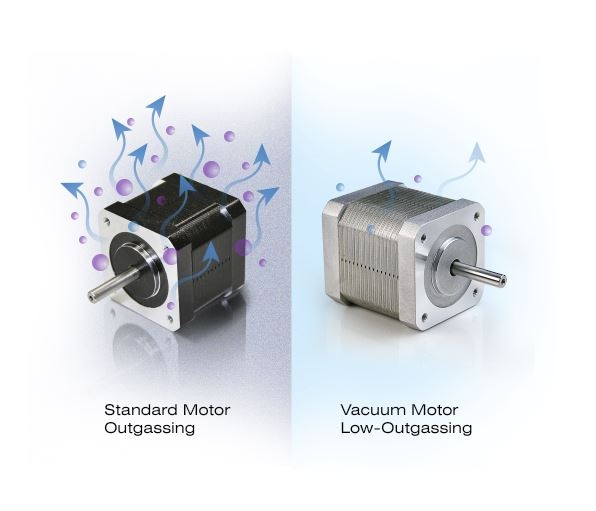
Vacuum Applications
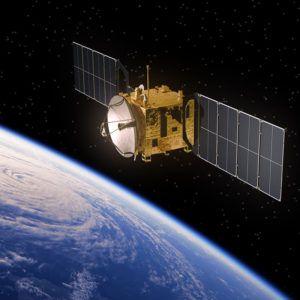
Specifically designed to be used in satellites and space craft, applications for our vacuum rated motors range from communication antennas to vehicle controls. We are an AS9100C registered manufacturer, and each motor is manufactured to meet the strict aerospace guidelines.