Load Calculations and Tips for Using Stepper Motors
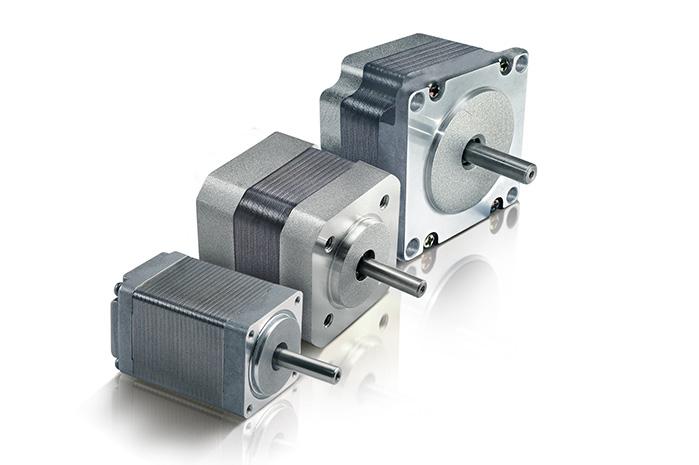
Load Calculations and Tips for Using Stepper Motors
To accurately provide load calculations for your next design, we’ve provided all the necessary formulas and concerns you might have. The following information presents important tips for anyone looking to incorporate step motors into their design. Below we’ve looked at standard load calculations, understanding speed/torque characteristics, some concerns when calculating acceleration torque, and information about the reduction of vibration and noise.
Load Calculations
The following equation is the one most commonly used when performing torque load (Tf) calculations.
Tf = G * r
where:
G = weight
r = radius
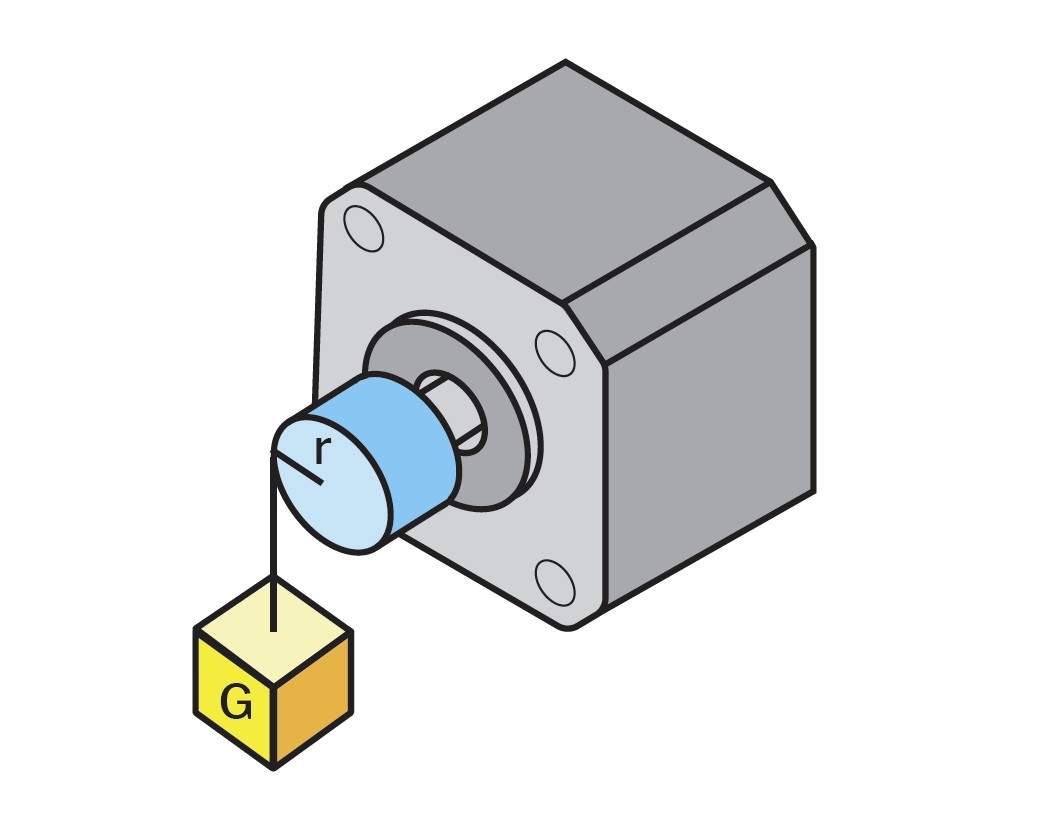
The following equations are the most commonly used when performing inertia load (TJ) calculations.
TJ = J * dw/dt
And J = M * (R12+R22) / 2 (Kg * cm)
where:
M = mass
R1 = outside radius
R2 = inside radius
dw/dt = angular acceleration
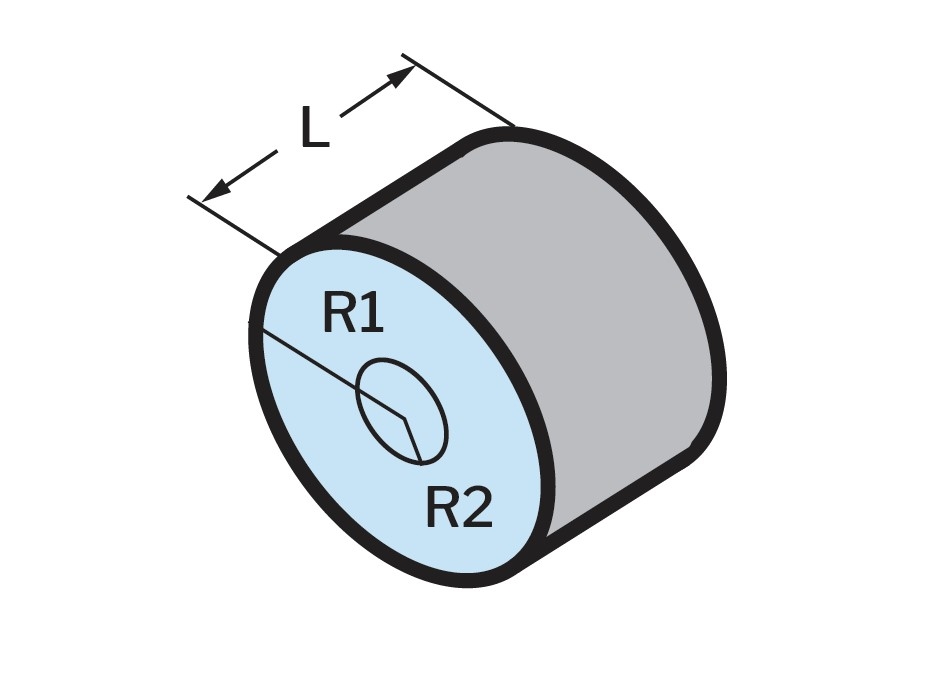
Understanding Speed/Torque Characteristics
An important aspect of a stepper motor’s output performance has to do with its dynamic torque curve. To better understand this curve, let us go through some key information.
A: The “working frequency point” expresses the step motor’s rotational speed versus its drive pulse rate. The following formula is helpful:
n = q * Hz / (360 * D)
where:
n = rev/sec
Hz = the frequency value or the driver pulse rate
D = the subdividing value of the motor driver
q = the step angle of the step motor design (e.i.: 1.8° step motor, in the condition of 1/2
subdividing (each step 0.9°) runs at 500Hz, therefore its speed is 1.25 rev/sec.
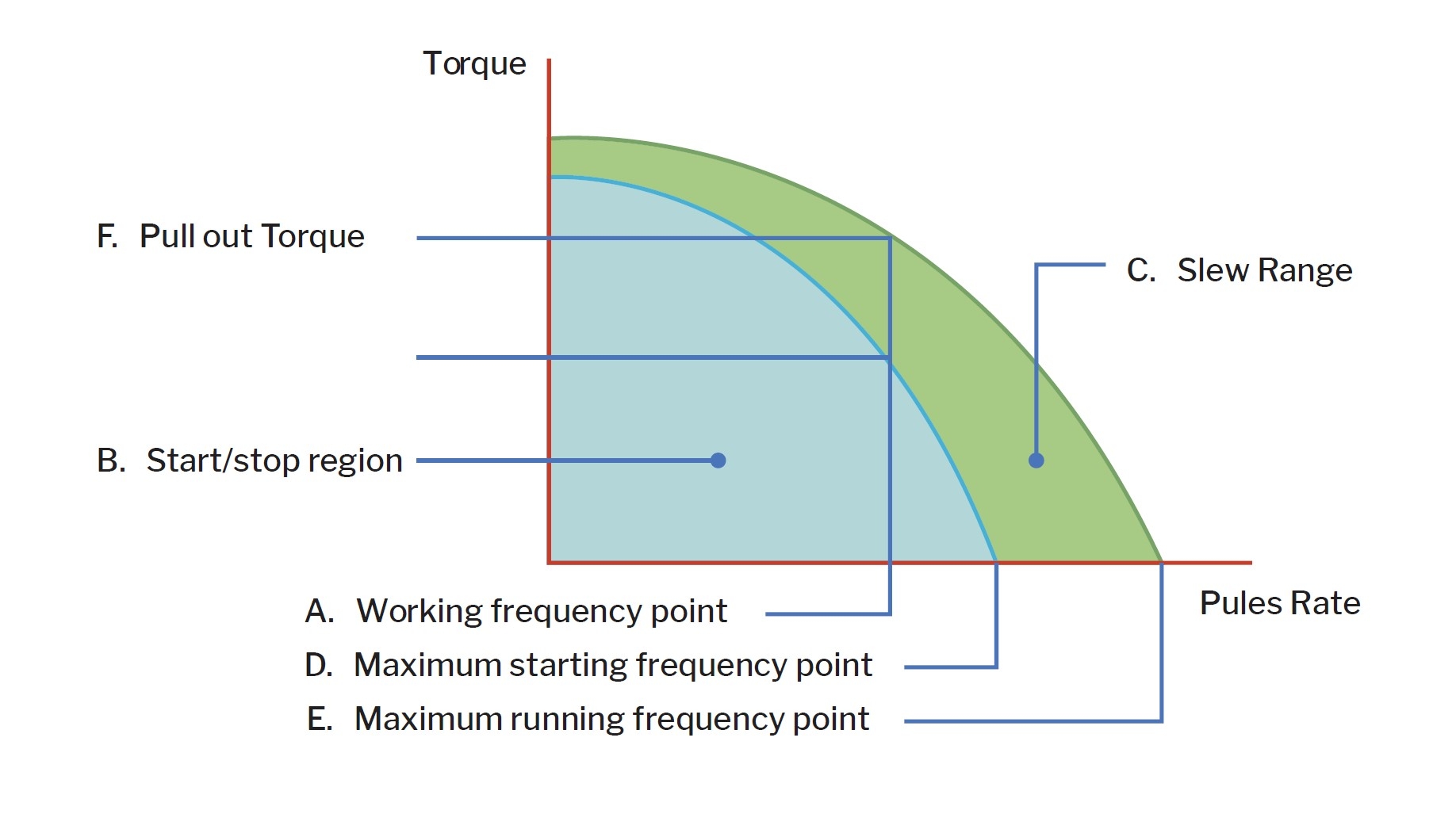
B: The start/stop region is the area in which a step motor can be directly started or stopped.
C: The slewing range, is the area in which the motor cannot be started directly. (It must be started in the start/stop region first and then accelerated into the slew range—in this area, the motor cannot be directly stopped, either or it would lead to losing steps.) The motor must be decelerated back to the start/stop region before it can be stopped.
D: Note that the maximum starting frequency point is the point at which the stepping motor can reach its maximum starting speed under unloaded conditions.
E: The maximum running frequency point is where the step motor can reach its maximum running speed under unloaded conditions.
F: Pull-in Torque is the maximum dynamic torque value that a step motor can load directly at the particular operating frequency point.
G: Pull-out Torque is the maximum dynamic torque value that a step motor can load at the particular operating frequency point when the motor has been started. (Because of the inertia of rotation the Pull- Out Torque is always larger than the Pull-In Torque.)
Acceleration Torque Calculations
The torque needed to accelerate the system inertia is often larger than the friction torque of the load. This fact limits how quickly the load can be accelerated.
As shown below, the dynamic torque performance of a step motor is constant at low speeds. Yet, at higher speeds, the torque drops as speed increases—influenced directly by the relationship between the motor inductance and the motor drive voltage. Note the following for a better understanding of these interactions.
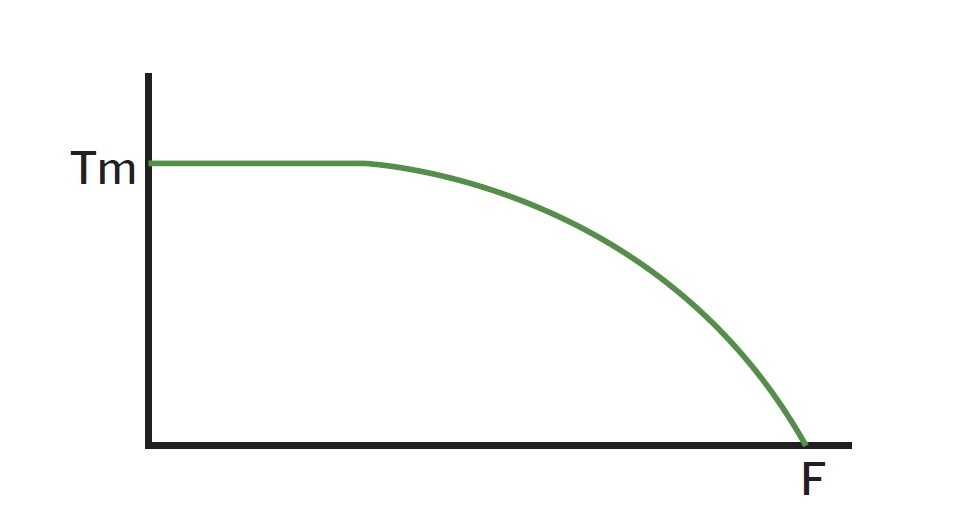
A: Accelerated Motion of Straight Line
The motor’s load value is known as TL and has to be accelerated from F0 to F1 in the shortest time period.
(tr), what is the value of tr?
(1). Generally TJ = 70%Tm
(2). tr = 1.8 * 10 -5 * J * q * (F1-F0)/(TJ-TL)
(3). F (t) = (F1-F0) * t/tr + F0, 0
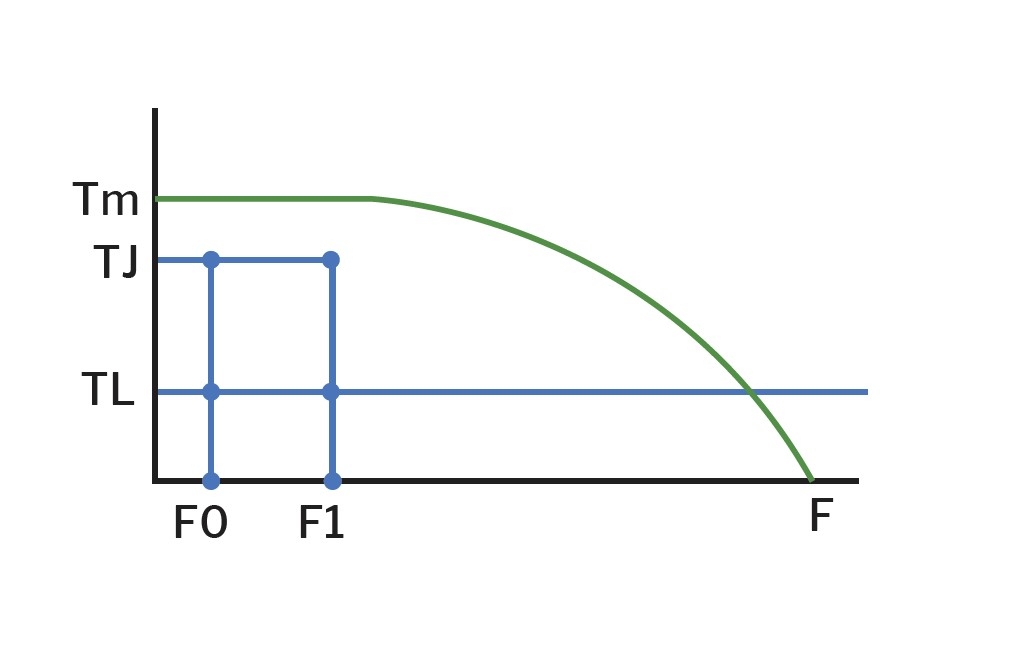
B: Exponential Acceleration
(1). Generally
TJ0 = 70%Tm0,
TJ1 = 70%Tm1,
TL = 60%Tm1
(2). tr = F4 * In [(TJ0-TL)/(TJ1-TL)]
(3). F (t) = F2 * [1 – e^(-t/F4)] + F0, 0F2 = (TL-TJ0) * (F1-F0)/(FJ1-TJ0)
F4 = 1.8 * 10-5 * J * q * F2/(TJ0-TL)
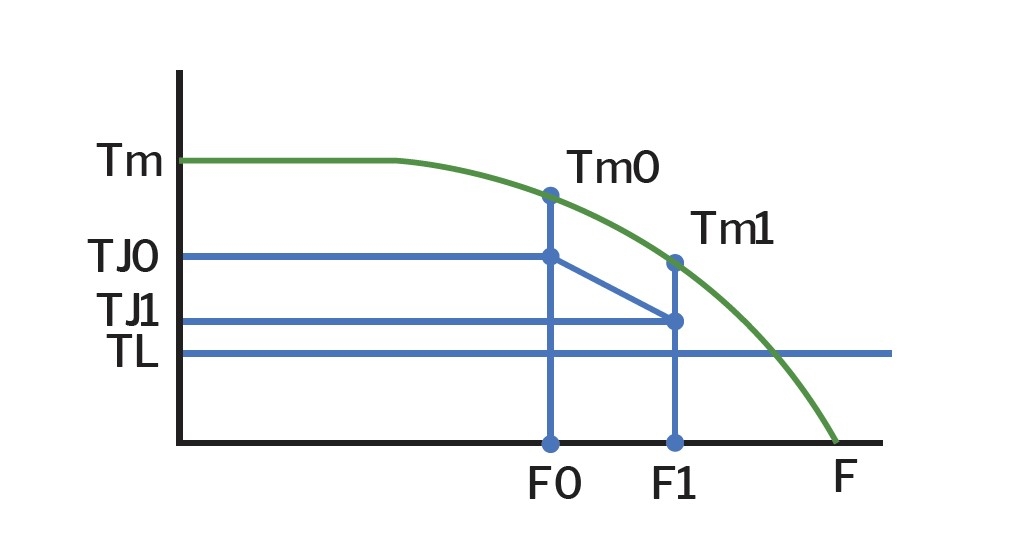
Note: J is the rotational inertia of the motor rotor plus the load, q is the angle of each step and is equal to the step angle of the step motor when the motor runs at full step.
Facilitating the Reduction of Vibration and Noise
In a no-load condition, step motors may appear to have a vibration or even lose steps when the motor is running at or close to the resonant frequency. There are several known solutions to this condition.
A. Simply be sure that the motor operates outside of this speed range.
B. Consider micro-stepping, which is used to increase a motor’s step resolution. By adopting a micro-step driving method, engineers can divide one step into multiple steps thereby greatly reducing vibration. This is accomplished by controlling the motor’s phase current ratio. Micro-stepping does not increase step accuracy; however, it will allow a motor to run more smoothly and with less noise. When the motor runs in half-step mode the motor torque will be 15% less than running in full-step mode. If the motor is controlled by sine wave current the motor torque will be reduced by 30% if using the same peak current.
C. Finally, you can reduce noise and vibration by incorporating a 0.9° 2 phase step motor or a three-phase step motor.
For more information:
News
Continue Reading
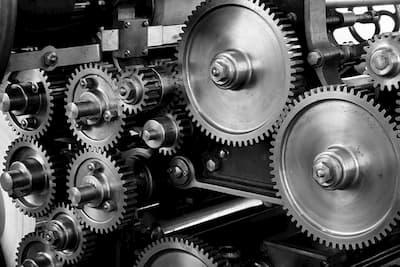
Multiple Ways to Increase Torque in Your Stepper Motor
Engineers continually need to cut overall costs, footprint, and maintenance requirements while continuing to design and build systems that must perform to tighter specifications and higher standards of operation. In talking with stepper motor experts from one company, it appears that a keen knowledge of motor workings is key.
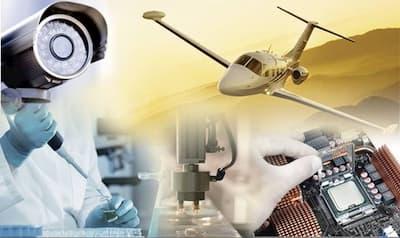
Get to Know Lin Engineering: Motor Specialist in Motion
Lin Engineering started in a garage—I’m sure you’ve heard that before. What may be more interesting is, unlike other companies that started in a garage, Ted Lin wasn’t creating a product, per se. He was adjusting a product to specifically perform in a certain way for a particular application. He was an innovator.